The Scientific Research Behind Porosity: A Comprehensive Overview for Welders and Fabricators
Understanding the detailed systems behind porosity in welding is important for welders and makers making every effort for remarkable craftsmanship. From the composition of the base products to the ins and outs of the welding procedure itself, a plethora of variables conspire to either intensify or minimize the existence of porosity.
Comprehending Porosity in Welding
FIRST SENTENCE:
Exam of porosity in welding exposes important insights into the honesty and high quality of the weld joint. Porosity, identified by the existence of cavities or voids within the weld metal, is an usual worry in welding procedures. These gaps, otherwise appropriately addressed, can jeopardize the structural honesty and mechanical properties of the weld, bring about possible failures in the completed product.
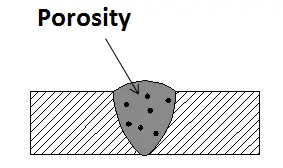
To spot and quantify porosity, non-destructive screening techniques such as ultrasonic screening or X-ray examination are often used. These strategies permit for the recognition of inner defects without compromising the integrity of the weld. By evaluating the size, shape, and distribution of porosity within a weld, welders can make informed decisions to improve their welding procedures and attain sounder weld joints.

Aspects Affecting Porosity Development
The incident of porosity in welding is influenced by a myriad of factors, ranging from gas protecting efficiency to the details of welding specification setups. One critical variable contributing to porosity development is insufficient gas protecting. When the protecting gas, usually argon or CO2, is not successfully covering the weld swimming pool, climatic gases like oxygen and nitrogen can infect the liquified steel, bring about porosity. Furthermore, the cleanliness of the base products plays a significant function. Pollutants such as rust, oil, or wetness can vaporize throughout welding, producing gas pockets within the weld. Welding parameters, including voltage, present, travel rate, and electrode kind, likewise influence porosity formation. Using inappropriate settings can produce too much spatter or warmth input, which consequently can lead to porosity. The welding method utilized, such as gas steel arc welding (GMAW) or protected steel arc welding (SMAW), can influence porosity development due to variations in warmth distribution and gas insurance coverage. Understanding and managing these factors are crucial for decreasing porosity in welding procedures.
Results of Porosity on Weld Quality
The presence of porosity also damages the weld's resistance to rust, as the trapped air or check it out gases within the gaps can react with the surrounding environment, leading to destruction over time. In addition, porosity can prevent the weld's capability to withstand stress or impact, more endangering the overall top quality and dependability of the bonded structure. In essential applications such as aerospace, vehicle, or structural buildings, where security and toughness are critical, the detrimental results of porosity on weld high quality can have severe repercussions, stressing the value of decreasing porosity with proper welding strategies and procedures.
Techniques to Decrease Porosity
In addition, making use of the appropriate welding parameters, such as this website the correct voltage, current, and take a trip speed, is vital in avoiding porosity. Preserving a regular arc size and angle during welding additionally helps decrease the chance of porosity.

Making use of the proper welding method, such as back-stepping or employing a weaving activity, can likewise assist distribute warmth uniformly and decrease the opportunities of porosity formation. By applying these methods, welders can properly reduce porosity and produce high-quality bonded joints.
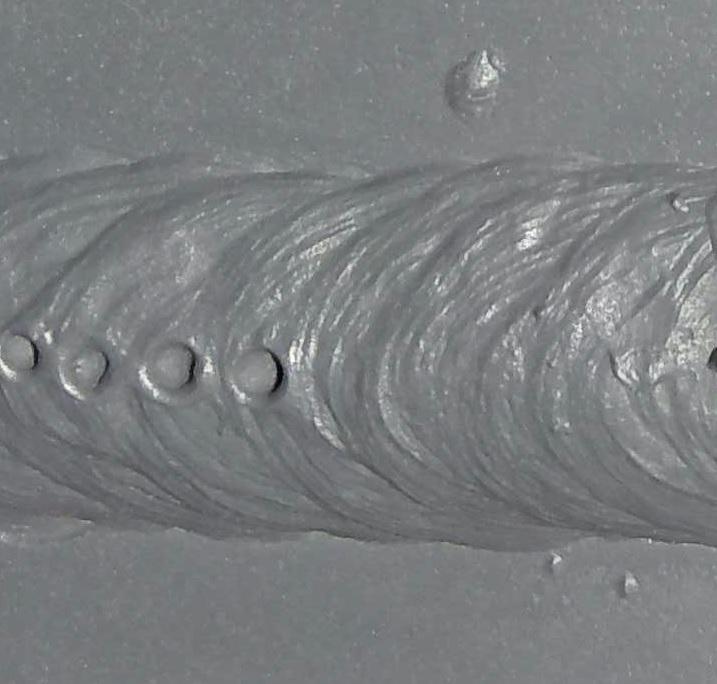
Advanced Solutions for Porosity Control
Implementing sophisticated innovations and innovative approaches plays an essential role in attaining exceptional control over porosity in welding procedures. One sophisticated solution is using sophisticated gas mixes. Securing gases like helium or a mix of argon and hydrogen can help minimize porosity by providing much better arc security and enhanced gas coverage. Furthermore, employing sophisticated welding techniques such as pulsed MIG welding or customized atmosphere welding can likewise help reduce porosity issues.
One more sophisticated option involves the use of advanced welding devices. Utilizing devices with built-in functions like waveform control and advanced power sources can boost weld quality and lower porosity risks. Moreover, the execution of automated welding systems with accurate control over specifications can dramatically decrease porosity flaws.
Additionally, incorporating innovative surveillance and assessment modern technologies such as real-time X-ray imaging or automated ultrasonic testing can aid in discovering porosity early in the welding procedure, permitting prompt restorative actions. Overall, integrating these advanced solutions can greatly boost porosity control and improve the general quality of bonded elements.
Final Thought
To conclude, understanding the science behind porosity in welding is crucial for welders and fabricators to generate high-grade welds. By determining the aspects influencing porosity development and carrying out techniques to decrease it, welders can enhance the overall weld click reference top quality. Advanced remedies for porosity control can even more boost the welding process and make certain a solid and trustworthy weld. It is crucial for welders to continuously enlighten themselves on porosity and execute best methods to achieve optimal outcomes.